Case Histories
Solving a Polymer Sealing Problem with XPS Analysis
Adhesive failure analysis is one of our special capabilities. We can determine the cause of adhesive bonding failures caused by exceedingly thin layers of contamination at interfaces using such capabilities as XPS surface analysis, contact angle measurements, FTIR, GC-MS, SEM, and optical microscopy. We can measure the strength of adhesive bonds with our mechanical testing capabilities.
Adhesive bonding failures are commonly said to be either cohesive failures or adhesive failures. A cohesive failure is a failure in the bulk layer of the adhesive or sometimes in the bulk of one of the adherends (material being bonded) and is usually the desired mode of failure. An adhesive failure occurs at the interface between the adhesive and the adherend. Such adhesive failures at the interface with all of the adhesive on one side of the separated materials is desired in some cases, such as in use with temporary notes, a peel-ply sheet on an adhesive film, a protective film, or a backing or support material on a roll of tape.
Silicones, primarily dimethyl siloxane, can cause adhesive or interfacial failures with only a fraction of a single layer of molecules, detectable quantitatively only with the extremely surface-sensitive XPS technique. Such low concentrations limited to the surface of other materials can cause similar adhesive bonding problems and not be detected by such methods as FTIR analysis or a Soxhlet extraction method. AME offers specialized silicone contamination collection kits which can be used to detect and measure silicone and other contaminants airborne in facilities or in ovens or deposited on facility surfaces with much greater sensitivity than provided by FTIR or Soxhlet extraction methods. The detection limit for poly(dimethyl siloxane) is about 0.007 mg/sq.ft. or about 0.08 mg per square meter. Significant adhesive bond strength loss often occurs at about 15 times these concentrations. These kits also measure other contaminants which are airborne or found on surfaces in facilities.
In many adhesive bonding failures, the reality is actually more complex. Failure which appears cohesive may occur due to degradation of the adhesive itself, such as by water or excessive heat or radiation. The adhesive may degrade by migration of fill materials, plasticizers, slip agents, or other additives to the surface over time. Apparent interfacial failures may be due to the prior excessive hydration of the adherend, whether it is metallic, glass, ceramic, or an inorganic particle. It might be due to a surface being excessively alkaline, since good adhesive bonding usually favors a slightly acidic surface. A classic case Dr. Anderson diagnosed was the excessively alkaline surface of glass microspheres in the thermal insulation of the Space Shuttle external fuel tank that once created a major crisis.
Many adhesives have a number of low concentration additives, which may segregate strongly to the interface forming a very thin layer at the interface of a highly different composition from the bulk adhesive. This thin and invisible layer may be desirable to strengthen the bond to the adherend surface, but improper application conditions may cause this thin interfacial layer not to form or to form incorrectly. Silane coupling agents and some amines are examples of adhesive ingredients that one commonly wants to migrate to the bonding interface in some optimal amount. Too much of these same ingredients may be bad, however. Some contaminants may be particularly capable of interfering with the formation of this needed thin layer of altered adhesive composition at the interface. As noted above, this migration can also be very bad, such as the migration of silica fill particles to a surface in an application due to a surface energy mismatch at the silica particle surface with the resin, excessive migration of amines, or the migration of alkaline sodium, magnesium, or calcium extracted from the surface of some fill particles. Migration of plasticizers or slip agents from polymer adherends to the surface over time can cause an interfacial adhesive failure. Degradation of the adhesive and/or the adherend/adhesive interface chemistry may be due to water ingress along the interface over time, which may precipitate an interfacial or adhesive failure. Hydrolysis attack of adhesives along a bondline, hydration of an inorganic fill material in either the adhesive or an adherend polymer, or the hydration degradation of a metal oxide layer can each occur over time either generally in a material or in the highly local zone of an interface. Such attack is common in adhesive bonding to concrete, which is usually an alkaline water environment, and is more generally common in warm and humid environments.
Adhesive failure analysis often requires sophisticated analysis to understand the cause of failure. The location of the failure may be in a very thin layer at an interface. The interface may have become contaminated during any of the processes used to prepare the adherend surface or afterwards. Fatal contamination layers are often less than 0.3 nm thick! One classic example is a silicone or dimethyl siloxane release agent or lubricant, which is what caused the failures at the frit interface in the above image. This thin layer of dimethyl siloxane was not detected by two prior laboratory investigations, but was readily detected in our laboratory using XPS surface analysis.
XPS analysis can distinguish silane coupling agents, dimethyl siloxane, diphenyl siloxane, silicates, and silica from one another. We can use it to classify dimethyl siloxane as either short chain length, medium chain length, or long chain length. Short chain length dimethyl siloxane is used in mold release agents and lubricants and can cause serious airborne contamination problems. See our facility monitoring service for detecting silicones and other contaminants in facilities performing high strength adhesive bonding. Analysis techniques such as Soxhlet extraction followed by FTIR or ICP-OES analysis only measure total elemental silicon and will produce false alarms due to the inability to distinguish siloxanes from silicates, silica, or silane coupling agents. Solvent rinsing of surfaces may not remove all of the silicone contaminant on a surface either.
Adhesives and organic coatings which are to adhere to surfaces are usefully characterized with FTIR analysis. FTIR commonly examines an adhesive or polymer to a depth of about 1 to 2 micrometers, or about 100 to 200 times deeper than XPS analysis does. It is useful to compare the composition at the surface of an adhesive as found by XPS analysis with that by FTIR to determine what in the surface composition is due to contaminants or to surface migration of species in the adhesive itself. Sometimes FTIR is even useful for detecting relatively thin layers of organic material that may either cause unintentional adhesion, such as in aluminum honeycomb processing where some areas are meant to bond strongly and some are not meant to bond at all, or in detecting thicker organic contamination layers that interfere with adhesive bonding. FTIR is also very useful in determining when general degradation of the adhesive is a problem, which may be caused by excessive water, contaminant, heat, or radiation exposure.
In other adhesive failure analysis cases, a metal surface may be treated to promote adhesion with a high surface area such as anodization processes, then treated to retard corrosion with a very thin layer of solid particles, and then treated with a silane adhesion promoter which may be thinner than 10 nm thick. Many things may go wrong in these processes. In other cases, a metal surface cleaning or de-scaling process may actually leave a residue on the surface. As little as 1 atomic percent of fluorine left by a hydrofluoric acid de-scaling process can cause a fatal accumulation of very hygroscopic aluminum fluoride over time and subsequent bond failure, for example. The heat treatment of a metal may drive impurities or low concentration component elements to the surface, such as carbon in the form of graphitic carbon or phosphorus, sulfur, and boron products which inhibit bonding.
Bonding to plastic, glass, ceramics, inorganic particles, or composite materials may suffer failures at or near interfaces for many reasons. Inorganic particle filler materials are often given treatments to promote polymer resin wetting, whether in composite materials, paints, adhesives, or sealants. When that fails in a composite material, the material is greatly weakened and the tendency of the fill particles to agglomerate or to migrate to the interface is enhanced. In a paint or sealant with such agglomeration, degradation due to UV exposure or peeling from the adherend can occur. Or, such inorganic particles may lose bonding due to excessive hydration. Glass surface bonds may fail if the glass surface was too alkaline when bonded, as Dr. Anderson demonstrated was the cause of Space Shuttle External Fuel Tank failures in the early 1990s. Metal surfaces, especially those with +2 valence states are inclined to suffer from excessively alkaline chemistries at surfaces also, especially as they hydrate. Plastic bonding may fail due to migration of plasticizers to the surface or residues of mold release agents, such as silicones or fluorocarbons.
Adhesive materials are often supplied with peel plies or plastic films to be peeled off prior to application of the adhesive. These peeled materials often leave silicone or fluorocarbon residues on the adhesive surface, which may seriously degrade the adhesive bond.
Adhesive Bonding Failure Example:
A client came to us with an aramid honeycomb structure that was experiencing bonding failure to an epoxy board with fiberglass reinforcement. It was determined that some areas of the honeycomb structure, prior to bonding, were contaminated. This contamination led to adhesive failure. The complex chemistry of the contamination was determined through XPS analysis.
Image Type | Successful Bonding Area | Failed Bonding Area |
---|---|---|
3D 50X Keyence Ring Photo | ![]() | ![]() |
Height Color Map | ![]() | ![]() |
Determine surface and interface chemistries using XPS surface analysis:
- Surface analysis of adherend or substrate material as prepared for bonding
- Surface analysis of both sides of peeled or failed interfaces to find locus of failure, identify interface chemistry, and identify any contaminants of adhesive failures
- Correlate surface chemistry of samples tested to failure with measured strength
- Examine aging and degradation effects on the chemistry at the interface as a function of time and exposure environment
- Determine differences of bondline adhesive chemistry from the bulk adhesive chemistry, since distinct and often radically different interfacial adhesive interphase layers are common
- Identify interfacial contaminants or degradation due to hydrolysis, silicones or siloxanes, plasticizers, surfactants, hand lotions, cutting oils, hard water deposits, solder fluxes, insufficient rinse of pretreatment acids or bases, mold release agents, and photoresists
- Provides the sensitive measurement of silicones and other contaminants found on clean surfaces of the returned Silicone Contamination Test Kits we send to facilities for airborne exposures and surface contamination transfer
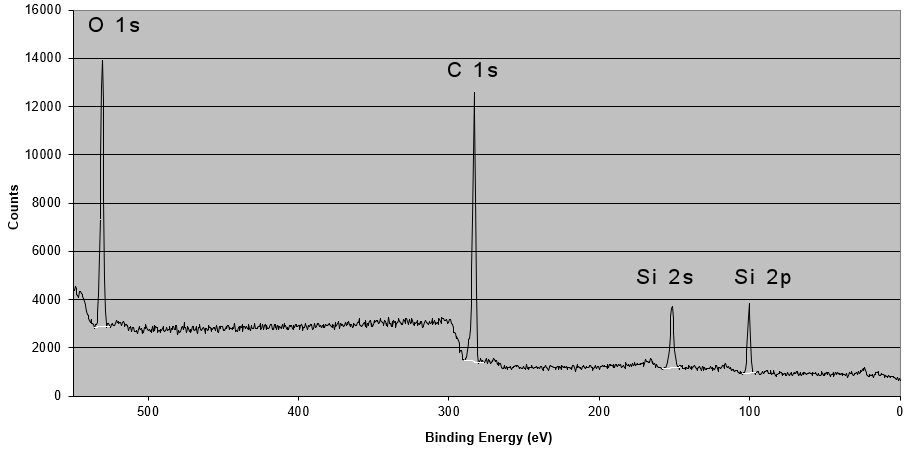
Prepare very clean adherend surfaces for reference to mechanically tested bond strengths of manufactured or prototype bonded materials.
Microscopy – SEM and Optical – Failure Analysis:
- Locates failure plane
- Indicates type of failure
- Reveals gas bubbling effects due to contaminants or improper 2-part adhesive mixtures
- Helps to choose best areas for XPS analysis or FTIR analysis
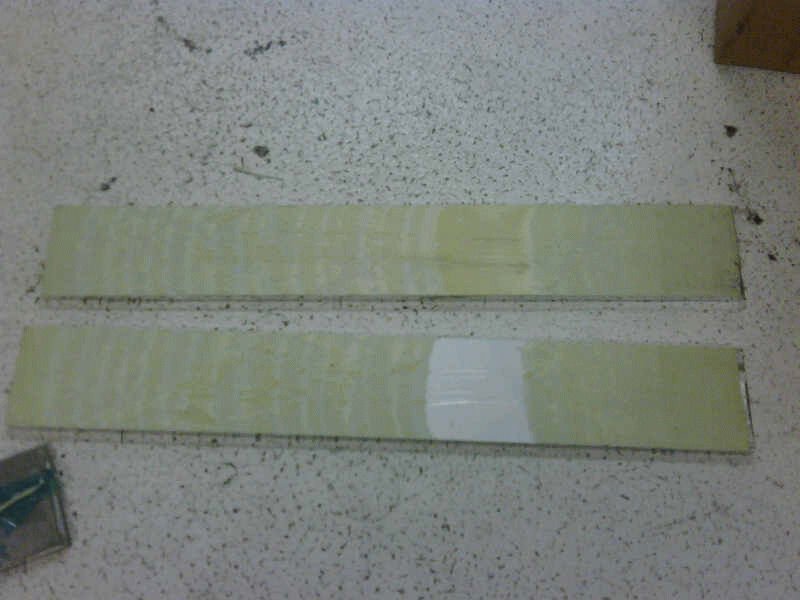
Thermal Analysis:
- TMA to determine differences of thermal expansion of adherends and adhesive since such differences may cause tremendous forces capable of ripping the adhesive bonds apart
- TMA to indicate whether thermoplastics have too much crystallinity, which may produce a large thermal expansion spike at the crystalline melting temperature
- TMA and DSC to determine maximum temperatures appropriate for curing adhesive bondlines or to prevent phase changes and degradation processes in use
- DSC to determine good adhesive curing conditions or problems due to improper mixtures of 2-part adhesives
- DSC to measure the degree of cure
Electrochemistry – Electrochemical Impedance Spectroscopy (EIS):
- Measures water concentration buildup in organic coatings and adhesives which can cause hydrolysis degradations of either the adhesive or the adherend surfaces
- Measures other ion concentration increases in coatings and adhesives over time that may indicate the corrosion of metal surfaces at the adhesive bondline with subsequent adhesion failures
- Measures effect of adhesive or coating pores, holidays, and fisheyes upon water reaching interface to cause hydrolysis attack of bondline
- Identify chemical differences at bondline interface relative to the bulk of the adhesive
- Contrast chemistry of 1 to 2 μm depth to that of the 10 nm measured by XPS
- Identify plastic, rubber, resin, and laminate materials being bonded
- Identify the adhesive and the primer to which adhesive is applied, as it is in aerospace adhesive bonds to aluminum surfaces
- With its ppb detection capability the cause of bonding failure may be directly detected in some cases with a quick solvent rinse of a failed interfacial area.
- Bond failures, particularly those that occur over time, are sometimes caused by the migration of a bulk plastic additive to the bonding interface. Leachable substances can be analyzed to determine if any have chemistries that might degrade the bond or to learn more about a chemical species detected by XPS or FTIR analysis.
- A more detailed understanding of the chemical species in an adhesive or sealant can be established. This may help to identify interface or surface segregating component materials and compounds that are incompatible with a polymer such as a polycarbonate.
- Very useful in determining which areas to further analyze with the above techniques
- Used to document the microscopic appearance associated with the subsequent results.
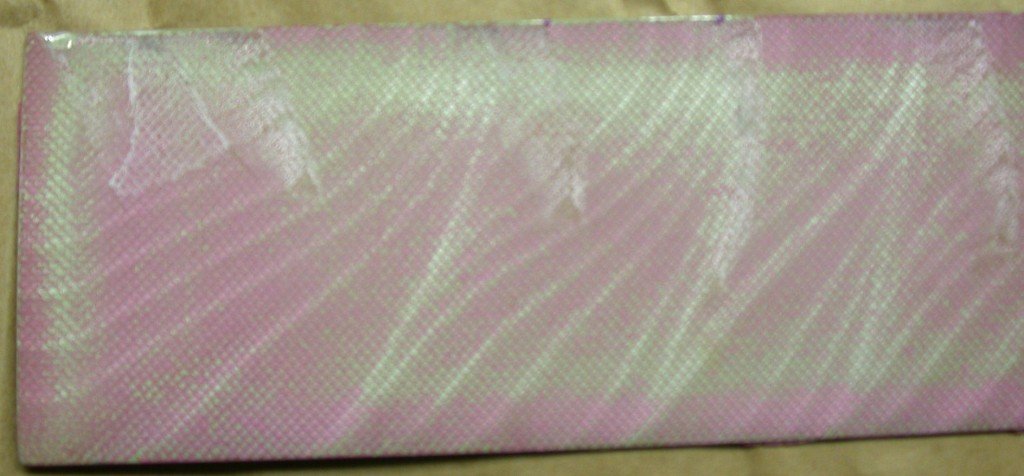
- Measure the tensile strength of an adhesive bond
- Measure lapshear strength of an adhesive bond
- Measure the peel strength of an adhesive bond
- Measure the bend durability of an adhesive bond
- Measure the carbon and nitrogen concentrations in adhesives and polymer adherends
- Measure the inorganic filler in an adhesive
Silicone Detection on the Surface of an Acrylic Adhesive/Polyimide Tape