A structural steel I-beam used as a rail in an overhead conveyor system was subjected to a nearly continuous over-spray of rinse water during standard operations. The rinse water had a neutral pH value. The operating environment was warm (78-85°F or 26-29°C) and humid (approximately 90% relative humidity). During a weekly break in operations a low pH liquid biocide was sprayed through the rinse water system as a standard maintenance procedure. Over a relatively short operational period the I-beam suffered severe general corrosion over all exposed surfaces. In addition, in the region where the contact rollers continuously passed over the I-beam surface there was a substantial loss of metal cross-section due to constant disruption of the corrosion layer and exposure of fresh metal. The I-beam was failing in its intended application in three ways:
- Poor appearance due to general corrosion,
- Flaking of rust onto the parts and equipment below, and
- Most importantly, raising safety concerns due to substantial thinning of a critical cross section.
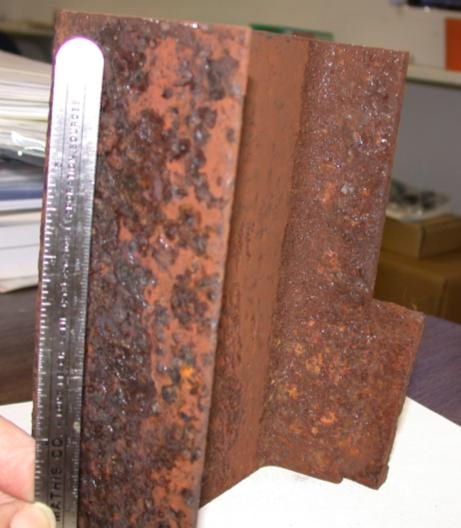
The biocide material, used to keep biological growth from occurring inside the water-spraying system, was suspected of accelerating the corrosion. The client tasked AME with determining whether the biocide was the cause of the accelerated corrosion, and whether the biocide or the I-beam material itself should be replaced. A section of the corroded I-beam was cut out and sent to AME for corrosion analysis. In this case a laboratory-controlled environmental exposure analysis was combined with potentiodynamic polarization. The combined techniques allowed us to observe the corrosion rate of the actual steel used onsite in simulated environments created using the actual onsite process water provided by the client.
For the exposure test two coupons were cut from the web of the I-beam section. These were ground flat on one face to a 200-grit finish. Suspension holes were drilled through each coupon. The two coupons were suspended over a heated bath of process water in a closed vessel, simulating the high temperature/high humidity environment encountered by the I-beam during normal facility operations. The coupons were periodically withdrawn and photographed to show the progress of corrosion on the finished faces. The table below gives the exposure times and conditions. The images clearly show the very rapid degradation of each surface. Severe general corrosion took hold in less than 48 hours.

After the completion of the exposure test Coupon #1 was again polished on one surface, this time to a final polishing step of 1 µm alumina. An electrical contact was made to the coupon. All unpolished surfaces, the electrical contact area, and the polished surface near the coupon’s edges were masked with a chemically inert coating, leaving an exposed polished area of 2.6 cm2. The prepared coupon was immersed in a fresh sample of process water heated to roughly 55°C for the potentiodynamic polarization measurement.
During potentiodynamic polarization a metal specimen is scanned through a range of potentials measured with respect to a stable reference electrode (here, a saturated calomel electrode – SCE). As the applied potential is varied the resulting current density (total current divided by exposed area) is measured. The specimen was first stepped to a potential known to be negative to its open circuit or corrosion potential, Ecorr. The applied potential was then swept through Ecorr and on to a more positive final voltage. At potentials below Ecorr the specimen is cathodic and so is protected from corrosion. Above Ecorr the specimen becomes anodic and is able to corrode freely in the electrolyte. The corrosion mechanisms may vary with the applied anodic potential. General corrosion begins around Ecorr. Consequently, the region of the cathodic-to-anodic transition yields the corrosion current density, icorr, which is used to calculate the instantaneous corrosion rate (ICR) associated with general corrosion. The results for Coupon #1 are shown below. This plot shows typical behavior for freely corroding iron in an aqueous electrolyte with ambient aeration. The ICR was calculated in mils per year (mpy) based on the assumption that iron was the only significant corroding component of the steel sample.
Based on the data and assumptions described above, an ICR of 15 mils per year was calculated for this steel when its clean surface was wetted with typical process water at elevated temperature. This corrosion rate can of course vary considerably in the actual working environment where the I-beam surfaces aged and built up corrosion product films, where these films were mechanically damaged by rollers, and where more aggressive solutions such as the biocide fluid occasionally made contact with areas of the I-beam. The much more rapid metal loss in the area of the contact rollers was due to the continual disruption of the corrosion product layer and the resulting exposure of fresh metal to the corrosive process environment.
The exposure test results show clearly that the steel coupons created from the I-beam section provided from the actual workplace corroded readily and quickly in an elevated temperature condensing humidity environment containing typical process water. It is highly likely that the aqueous low-pH liquid biocide also played a role in accelerating the corrosion of the rail. However the sheer number of hours spent by this rail in the normal process environment compared to roughly one hour per week of exposure to the biocide fluid must be considered. This time differential coupled with the poor performance of the steel in laboratory tests conducted in process water alone is a strong argument that the main cause for the excessive corrosion was the normal rinse process itself.
Based on the exposure testing results AME suggested a change in the I-beam conveyor rail material. The client selected a stainless steel material with greater corrosion resistance properties as well as the mechanical properties needed to perform the function.
Direct questions regarding electrochemistry and corrosion testing to Dr. Lorrie A. Krebs