At Anderson Materials Evaluation, Inc., we specialize in silicone contamination testing for facilities and ovens. Our comprehensive testing services include providing special collection kits, which allow for finding and identification of silicone and fluorocarbons as contaminants. We also offer direct analysis of parts or samples for contamination if that is what your company needs. At our lab, our team of experienced Ph.D. scientists can help you identify the cause of your contamination issues so that your business can get back on track.
Silicone Contamination Collection Kits
Our silicone contamination collection kits are designed to be silicone-free. They enable sensitive measurement of silicone in your facility. Once you return the kits to our laboratory, we use XPS analysis to determine the specific types and concentrations found. This advanced test method helps find levels of silicone that can cause significant adhesive bonding failures, surface wetting problems, and sealing issues. This is why it is important to test your materials for contamination issues.
Why Silicone Contamination Testing is Essential
Silicone contamination can lead to severe problems with your materials, such as:
- Adhesive Bonding Degradation: Silicone contamination can affect adhesive bond strength, leading to failures in bonds.
- Surface Wetting Issues: Silicone can prevent proper surface wetting by adhesives, sealants, and coatings which can lead to failures.
- Optical Element Contamination: Exposure to UV and blue light breaks down silicone materials, leaving harmful particles on optical elements.
Testing for these problems often and early can save your company both time and money.
XPS Analysis for Silicone Contamination
XPS analysis of the kit test surface distinguishes sources of silicon, including:
- Silica or glass
- Silicates
- Different types of siloxanes such as:
- Diphenyl siloxane
- Long chain length dimethyl siloxane (sealants or electronics encapsulants)
- Medium chain length dimethyl siloxane (pressure sensitive adhesives)
- Short chain length dimethyl siloxane (lubricants or mold release agents)
- Very short chain length dimethyl siloxane (lubricants or mold release agents)
- Extremely short chain length dimethyl siloxane or small molecule silicones
- Silane coupling agents
The most common silicone contaminant is polydimethyl siloxane, also known as PDMS. Short chain dimethyl siloxanes are particularly harmful as they spread easily, covering more surface area and stopping proper adhesion of surfaces. This is why it is essential to identify the type of silicone contamination that may be affecting your materials processes.
Preventing Silicone Contamination
Understanding the chain length of PDMS is crucial for finding the contamination source and stopping repeat issues. Cleaning silicone contamination can be costly and take a lot of time to fix, often causing product failures. Testing your materials early and often can prevent these costly problems.
What Our Testing Kits Can Be Used For
We offer kits for various reasons:
- Facility Airborne Contaminants: Suitable for temperatures below 60°C (P/N SILTK-AA3)
- Airborne Contaminants in Heated Environments: For temperatures above 60°C (P/N SILTK-HT2)
- Surface Contaminants: Detect contaminants on walls, floors, and production equipment (P/N SILTK-TT2)
These kits are designed to find silicone contamination and ensure materials are proven to be silicone-free. XPS surface analysis measures silicon concentration with a detection limit of about 0.2 atomic percent (at.%), and down to 0.1 at.% with ambient airborne collection kits. Using these kits can help you identify contamination early and avoid bigger issues financial issues down the line.
Importance of Accurate Measurement
Silicon at 0.2 at.% in the form of PDMS equals about 0.007 mg per square foot, or 0.08 mg per square meter. Significant adhesive bond strength loss usually occurs at about 3 at.% silicon in dimethyl siloxane form, which is about 15 times the detection limit of our kits. Accurate measurement is crucial to keeping up product quality.
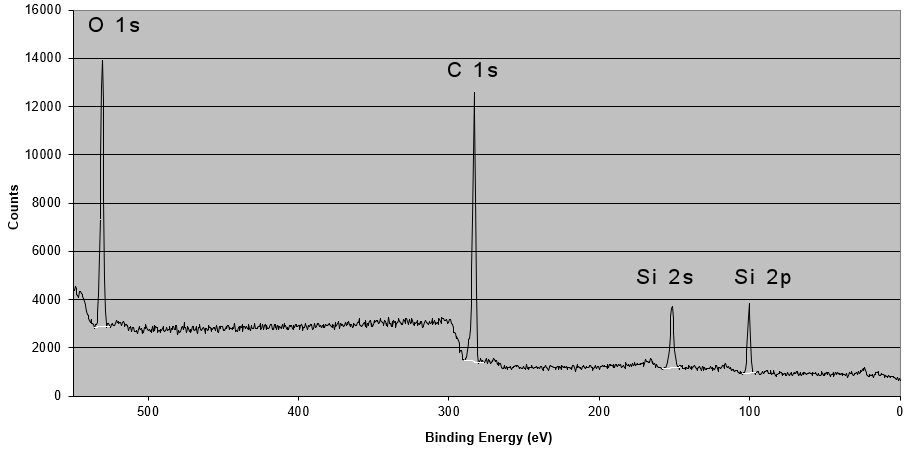
Additional Testing Capabilities
Our kits can also measure fluorocarbon contamination and nitrogen organic contaminants on surfaces or airborne. The kits protect the exposure surface from contamination during the shipment of the sample, making sure you get accurate analysis. This comprehensive approach ensures you get reliable results.
Alternative Testing Methods
For silicone contamination testing by the Soxhlet method, we offer improved procedures based on Rohr testing methods. However, XPS testing remains superior for finding small concentrations of silicones, providing better identification and sensitivity. This means you get more precise and detailed results to help get your business and it’s products back on track.
Contact Us for Silicone Contamination Testing
For assistance with your possible silicone contamination testing needs, contact Charles R. Anderson, Ph.D. directly at canderson@andersonmaterials.com or complete the form on our “Contact Us” page. We are dedicated to helping you with all your testing needs and are ready to answer any questions you may have. Our detailed and comprehensive results will ensure that your company can swiftly return to its most efficient operations.